The frontline
how-to platform.
Hassle-free coordination of frontline knowledge.
CROWDSOURCE SILENT KNOWLEDGE
Capture knowledge from your frontline experts.
Collect expert knowledge with crowdsourced digital work instructions and SOPs. Checklists and approval workflows ensure compliance and quality. Create content with the help of AI.
-
Proven Templates.
Our instructional design and technical documentation templates are based on proven academic research. Reduce authoring time by 80%.
-
Drag & Drop.
Easily edit instructions on mobile and tablet devices at the production line or in the field.
-
Checklists & Sign-off.
Capture performance data with checklists.
Use sign-offs to confirm task completion. -
Approval Workflows.
Make sure content is reviewed by the right people in the right order before it's distributed on the frontline.
-
Teams & Users.
Assign roles to your team and decide who can administer or edit content.
Platform Admins, Admins, Editors, Viewers, and Approvers all have access to the platform, but dispose of different permissions, providing a clear structure and a secure work environment.
-
Versioning.
Keep a current, live version of your guides while simultaneously making edits and changes in a new draft. Check previous versions and see what changes have been made to keep track of recent improvements.
-
Revision History.
Make sure your guides are up-to-date and checked on a regular basis. Set up a standard reminder cycle to ensure periodical reviews of your guides.
-
Languages.
Editors can use their native language when creating content: English, Bulgarian, Chinese, Czech, Dutch, Finnish, French, German, Greek, Italian, Norwegian, Portuguese, Romanian, Russian, Spanish, and Vietnamese.
Instructions can be translated into any left-to-right notated language. To date, our customers have created instructions in 43 languages.
-
SSO.
Login with your company account: Oauth2, Azure AD, Google, or SAML2.
50%
faster task completion with SwipeGuide.
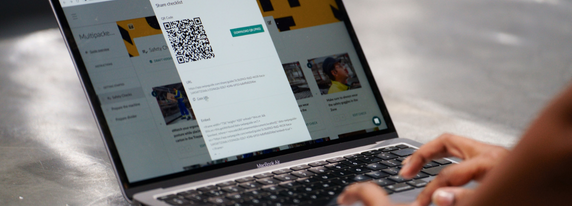
The AI-Powered Instruction Builder.
✓ Smart content management powered by AI.
✓ Create, edit, and publish instructions and checklists in seconds.
✓ Available for tablets and desktops.
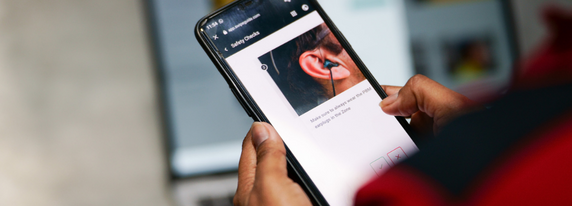
Checklists.
✓ Safety checklists for frontline teams.
✓ Track work execution and capture operational data with digital checks.
✓ Monitor adherence to company standards and capture deviations.
SCALABLE BEST PRACTICES
Share best practices.
Instantly distribute standardized operational knowledge across sites and production lines to whoever needs it, whenever they need it.
-
QR, Embed, NFC & Links.
Use QR codes, NFC, direct links, or embed to share instructions. Link the right information directly to the job.
-
The Frontline App.
Our Frontline App can be used both online and offline on any compatible device.
-
Tagging & Search.
Create a tag and badge system to organize and find your instructions quicker. You can easily organize and label them for effortless searches.
-
Share Best Practices.
Best practices can be shared within your company by making guides available for copying to other workspaces.
Simply copy and reuse great content from other parts of your organization. Benefit from the good work already done by others and avoid double work.
-
Offline Access.
The SwipeGuide Frontline App can be accessed on any device and used offline.
The app will automatically download the latest version of any work instruction when connected to the internet.
-
Secure Access.
Within the SwipeGuide platform, you can create independent workspaces for your teams and sites. The roles and permissions assigned to team members allow you to administer access and rights.
-
Multi-Space.
Allow your organization to create, share, use, and improve standards to create truly global success.
-
Phones, Tablets & Wearables.
Create and open instructions on any mobile device. SwipeGuide supports all iOS and Android devices.
-
Operating Systems.
Both Android and iOS are supported, both online and offline.
All standard browsers are supported.
31%
skill improvement of frontline workers.
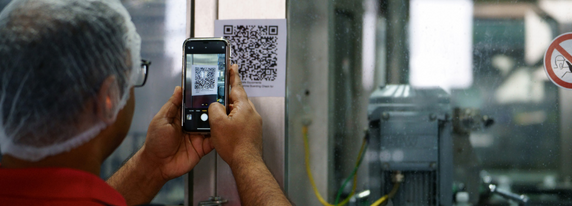
Knowledge Sharing.
✓ Share best practices across sites and locations.
✓ Re-use instructions, SOPs, and checklists that has already been created.
✓ Localize standards to your team's needs.
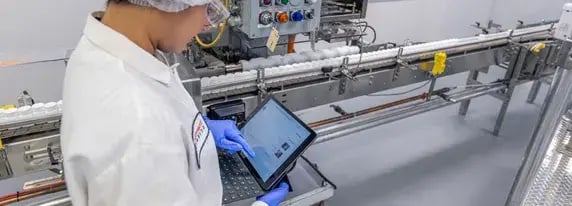
Offline Availability.
✓ Access your digital work instructions anywhere.
✓ No internet required.
✓ Available both for iOS and Android on any smartphone or tablet.
CONTINUOUSLY IMPROVE PROCESSES
Improve people. Improve performance.
Facilitate continuous improvement and track performance metrics including 5S, OEE, and FTR to achieve your operational excellence goals.
-
Knowledge Analytics.
See how your content is being used and how it's impacting performance in terms of efficiency, productivity, and downtime reductions.
-
Integrations & API.
You can connect SwipeGuide with your ERP, MRP, or MES by using our robust API or custom integration.
Read more about partners and integration options here.
-
Time Tracking.
Track the time spent on each step, instruction, and topic while monitoring completion rates.
Find out how long it takes users to complete their tasks to increase efficiency.
-
Instruction Feedback.
Gather insights from users on your instructions and procedures. Identify pain points and improvements in instructions instantly by collecting feedback using instruction scoring or more detailed text answers.
-
Content Migration.
We migrate your existing content into SwipeGuide.
-
Your Success Manager.
If you choose the Enterprise package, a dedicated Customer Success Manager will support you during and after the onboarding process.
-
24/7 Support.
Our Customer Support Team is available at all times via chat, email, or an emergency phone number to help you with urgent matters and minimize problem-solving time.
61%
reduction in product errors.
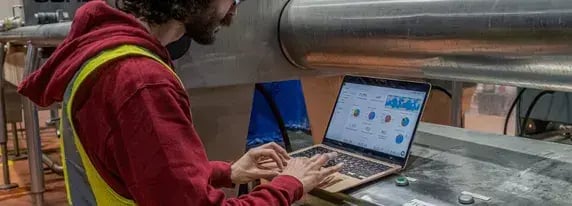
Insights & Data API.
✓ Compare data across teams, lines, and sites.
✓ Get actionable data and insights on how SOPs are used.
✓ Connect to your data visualization tool or data lake to uncover patterns, optimize processes, and make data-driven decisions.
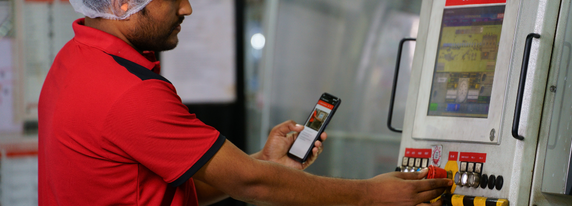
Audit Support.
✓ Standardize processes for compliance.
✓ Perform tasks safely.
✓ Ace your audits every time.
ONBOARD, UPSKILL, RETAIN, REPEAT
Self-directed skills development.
Easy access to on-the-job learning content that helps operators learn the skills needed to keep up with expectations and progress their careers.
-
Skills portfolio
Personal skills portfolio with proof of competence and training.
→ Track skills development.
→ Access status and levels.
→ Collect certificates of training & skills. -
Learning content
Develop new skills with self-directed learning content and activities.
→ Self-directed learning.
→ Reach higher skill levels.
→ Save your favorites. -
Self-assessments
Assess your own skills and get them approved by a manager.
→ Test your own knowledge.
→ Request a review from a manager.
→ Collect certificates. -
Updates
Receive notifications about important updates.
→ Assessment status.
→ New learning content.
→ Expiring skills. -
Learning journeys
Plan your personal career development path. See what it takes to reach your goals.
→ Skills vs. roles.
→ Training plans.
→ Exceed expectations.
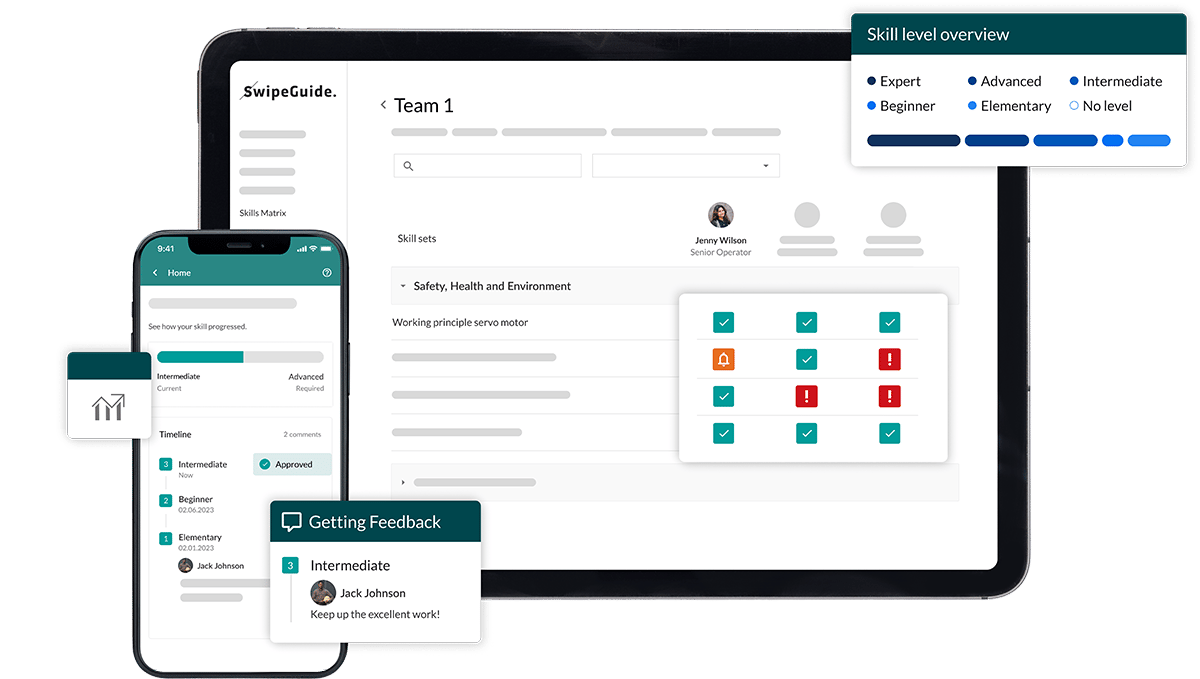
ALL CAPABILITIES - ONE OVERVIEW
Skills management
made easy.
Efficiently manage skills, streamline operations, and validate training with dynamic skills matrices. Ensure 100% performance and compliance across all teams.
-
Skills frameworks
Configure skill frameworks to match the levels used in your organization.
→ Skills and competency levels.
→ Adaptable skills profiles.
→ Compare performance. -
Skills matrix
Coordinate the skills of team members in a Skills Matrix that adjusts automatically.
→ Coordinate skills of teams and individuals.
→ Map out skills gaps.
→ Validate certification. -
Skills assessment
Assess skills of your team to prove skills development and competence.
→ Validate skill levels.
→ On-the-job assessments.
→ Review self-assessments. -
Content management
Create and manage adaptive learning content in Learning Libraries. Add materials from other systems.
→ Clear onboarding and learning journeys.
→ Create learning libraries per role.
→ Fill skills gaps. -
Certification
Keep track of when skills are expiring with certificates.
→ Track expiration of skills.
→ Plan re-assessments.
→ Set up training plans. -
Capability search
Find certified colleagues based on their skills and qualifications.
→ Flex your workforce.
→ Find replacements.
→ Rotate team members. -
Skills intelligence
Data-driven insights based on skills development progress.
→ Track progress across the organization.
→ Follow development over time.
→ Identify how training can improve.
4
hours saved on skills management every day