
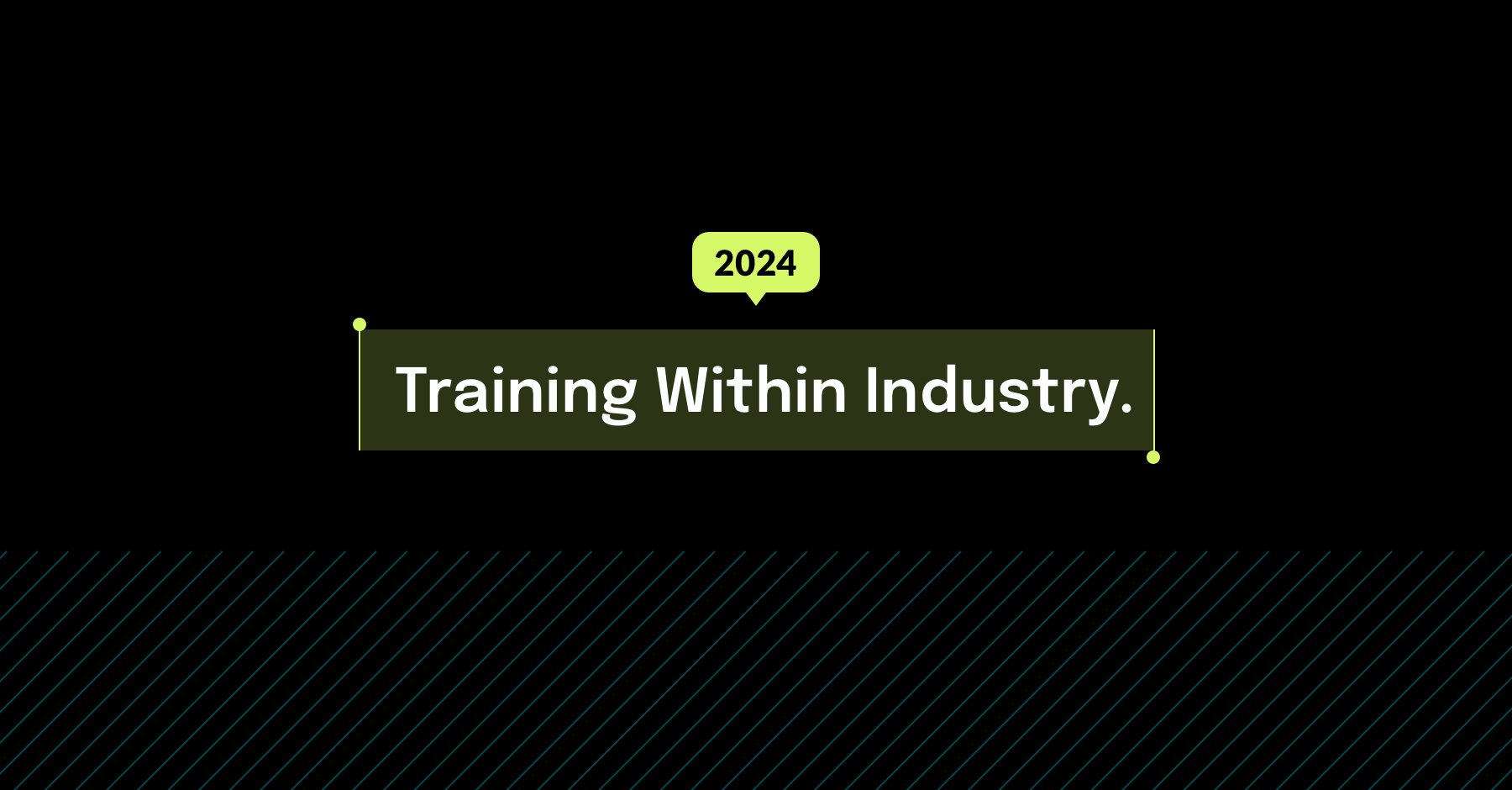
The Meaning of Training Within Industry (TWI) in the 2020s.
Training Within Industry (TWI) has been around since the 1940s. Some things are outdated, but the idea is still relevant in the 2020s - Let's dig deeper!
What is Training Within Industry?
Training Within Industry (TWI) = practical hands-on learning while working.
Training Within Industry is an effective method to train frontline workers, supervisors, and team leaders through hands-on learning and coaching. Its principles are a great way to improve the skills, safety and stability needed to drive efficiency in the workplace.
TWI was created in the 1940s to train the massive amount of new workers needed to sustain the US war effort during World War II. As the previous working force was sent to the front and the demand for war material remained high, it was essential to quickly train new professionals to fill in for those deployed to the frontline and maximize output while minimizing personnel, taking both quantity and quality into account.
💡 Knowledge sharing for continuous improvement. A major aspect of what made Training Within Industry so successful is the emphasis on cumulative knowledge. Experienced professionals passed on their knowledge to create a cycle of knowledge sharing to ensure its full integration into the company culture.
The results spoke for themselves. Based on a sample of 600 plants monitored from 1941 to 1945, all of them reported at least a 25% improvement in reduced training time and reduced grievances, and around 86-88% reported increased production and reduced labor hours.
Times have changed. Our needs are different and technology has evolved, but the point remains the same: the fundamentals of training within industry are still applicable at the frontline, and will help companies boost efficiency and productivity.
How to implement Training Within Industry.
Here are 5 elements which shape TWI and are still very relevant today:
- Standardization
- Collaboration
- Structure
- Accessibility
- Continuous improvement
☝️ PS. Did you know that TPM, Kaizen, and many other Lean philosophies are based on the original principles of TWI?
01. Standardization.
We all want to make manufacturing processes smarter, faster, and more productive. The best and the brightest in the business know that in order to achieve success in such a complex industry, work must be standardized.
Standard Work impacts all elements of the manufacturing supply chain by ensuring the consistent quality of the product and the efficiency of the individual worker. A lack of standardization frequently results in:
- High operational costs: Unplanned downtime and longer changeover times, both caused by non-standard work, are incredibly expensive.
- Difficult training: Outdated or incorrect information can result in ineffective, costly, and frustrating learning experiences for workers.
- Increase in product defects: Sub-par training and inconsistent processes lead to more mistakes on the shop floor.
However, if the company standardizes its process, it
- Saves time and increases output: When new employees have access to a standardized and documented process, it decreases the reliance on other team members and eliminates the need to spend time recalling each step for every task.
- Simplifies training: It becomes easier and more effective to train, as new employees can quickly learn and adapt to established protocols, reducing onboarding time and errors.
- Reduces errors and oversights: Standardized processes enable organizations to maintain and improve quality standards by providing clear guidelines and best practices for performing tasks or delivering services.
As manufacturing processes become faster, more complex, and increasingly digitized, learning on the shop floor needs to facilitate standard work and keep pace with the new world of industry 4.0.
02. Collaboration.
Training Within Industry pairs one student with an expert. The idea is that individual time and attention is paramount in the learning process because it allows learners to receive individualized mentorship and feedback while also performing a task in parallel.
Sounds great BUT....
- Today, factory teams are struggling with limited time and resources.
- Usually, senior experts cannot give this individual attention to all trainees.
- Roles for factory team members are becoming more and more complex.
Collaboration is still important, but in a modern and digital way:
- Frontline team members can be involved in shaping processes together.
- Digital on-the-job training and onboarding reduces training time and cost.
- Team members can collaborate on creating, sharing, and improving best practices across teams, lines, and even sites.
03. Structure.
Many say that content is king.
However, research shows that a great structure is the real king for a positive and successful learning experience.
Think about the following structure elements when creating training materials like including work instructions and SOPs:
- Taxonomy: use logical instructional design templates.
- Clarity: focus on the task at hand (aka don't describe the machine).
- Action: use action-oriented words ("press", "use", "turn knob to the left"...)
- Split it up: Step-by-step makes it easier to perform tasks.
- Visual: Always use visuals to explain the step.
04. Accessibility.
In addition to optimizing the structure and process of instruction, TWI provides learners with the essential information necessary to complete a task successfully.
Great instructions made in accordance with TWI should:
- Be consistent and easy to understand.
- Be easy to access at the moment of need.
- Make it as easy as possible to complete the task.
- Outline the necessary materials needed.
- Mention the time needed to complete any task.
- Lay out safety hazards related to the task.
- NOT be an "information overload."
05. Continuous improvement.
One reason TWI methodology remains relevant is that it has always adapted its time. TWI programs are designed to continually make processes more effective and efficient. Just like the Kaizen philosophy, Training Within Industry demands the continuous re-examination of processes and procedures.
With every new improvement and redesign, organisations:
- Foster a work environment that values the opinions of the workforce.
- Motivate and engage employees.
- Work to actively implement new ideas and improvements.
- Knowledge is democratized to optimize all aspects of operations
Implementing Training-Within-Industry will empower employees to excel in their roles, drive success and deliver exceptional results for the organization. Embracing TWI not only cultivates a culture of excellence but also ensures sustained growth and competitiveness in today's dynamic business landscape.
☝️ Remember: Don't get stuck in the past.
Want to learn more?
👉 What is a SOP?
👉 How to create smooth frontline training programs.
👉 Inspirational Kaizen Quotes to Motivate Your Team.
Author
Revisions
It's time to simplify frontline training
Work instructions, checklists, and skills management - all in SwipeGuide
- Cut training time by 50%
- SOC I and II compliant