5S in a nutshell.
The 5S (or five s’s) is often the first lean method organizations implement when they commit to ongoing process improvement. The method was first developed in Japan as a means to enable just in time (JIT) production. 5S is often talked about in the context of Kaizen, lean six sigma, and standardization.
5S stands for:
1. Sort
2. Set in Order
3. Shine
4. Standardize
5. Sustain
You might also come across the original five s’s in Japanese: seiri (整理), seiton (整頓), seisō (清掃), seiketsu (清潔), and shitsuke (躾).
5S Standard Operating Procedures.
1. Sort
First, you start by sorting out the "mess."
Typically, organizations use a system called “red-tagging” to identify unnecessary items and ensure quick sorting and removal.
By removing unnecessary items from the production area and organizing essential ones efficiently, Sorting leads to improved productivity, easier workflows, and a more organized and efficient work environment.
What helps? Accessible and digital standardized work instructions.
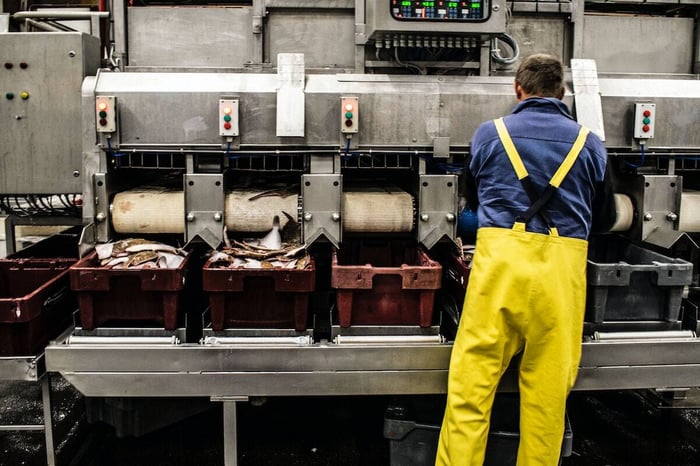
Access and structure are key when talking about the "sorting" aspect of 5S Standard Operating Procedures.
2. Set in Order
Next, order.
Organizing the items you need and putting them in the optimal place minimizes wasted time searching for tools or materials. This allows teams to quickly locate what they need, leading to smoother operations and faster task completion.
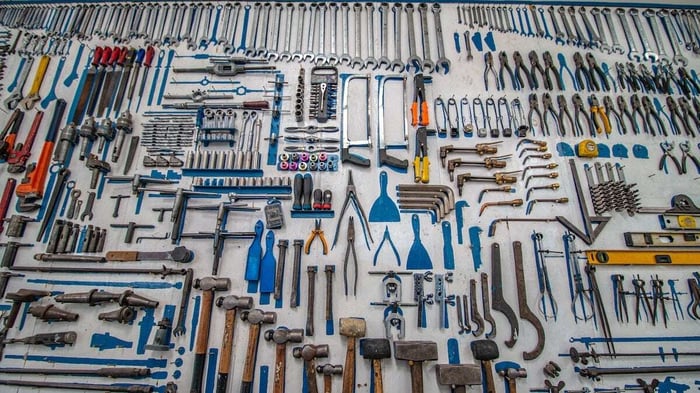
The location and visibility of 5S standard operating procedures is crucial when "setting in order".
3. Shine
Once everything's sorted out and organized, you need to make sure your workplace is clean.
The importance of cleanliness cannot be understated, especially if you’re dealing with expensive equipment.
Maintaining tidiness with regular cleaning and inspection enables employees to notice equipment malfunctions or misalignments quickly and avoid contamination or quality breaches.
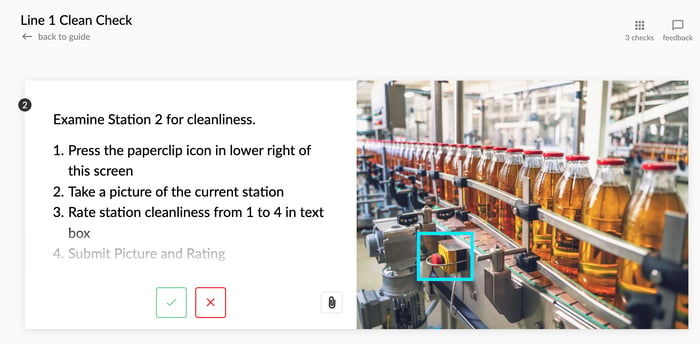
Checklists provide practical guidance of cleaning inspections in the "shine" aspect of 5S SOPs.
4. Standardize
To boost continuous improvement and innovation within your organization, making it tidy isn’t enough. You need to provide a consistent and clear plan that employees can follow.
Standardization ensures uniformity and reliability in operations, reduces variability and errors, and facilitates training and onboarding for new employees.
Read more about standardization in these articles:
Standardization is the base for consistency and continuous improvement in 5S operating procedures.
5. Sustain
Last but not least, you need to make 5S a habit.
Simple step-by-step instructions will make it easier for employees to embrace these best practices and can help smoothly integrate them into daily working routines.
For example, using a tablet with digitized procedures instead of long and dusty manuals.
Learn more about 5S and SOPs:
👉 Standard Operating Procedures (SOP) Best Practices & Guidelines.
👉 Standard Work = Processes + Procedures + Work Instructions.
👉 Empowering a Culture of Operational Excellence
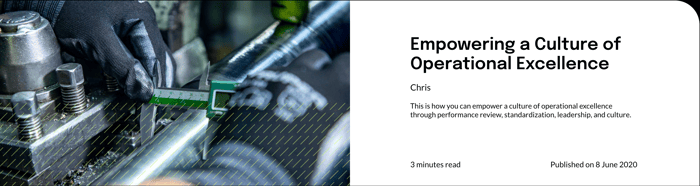