![Employee Development Plans Boost Frontline Retention [Template]](https://www.swipeguide.com/hubfs/SwipeGuide_March2025/Images/Employee-Development-Plan.webp)
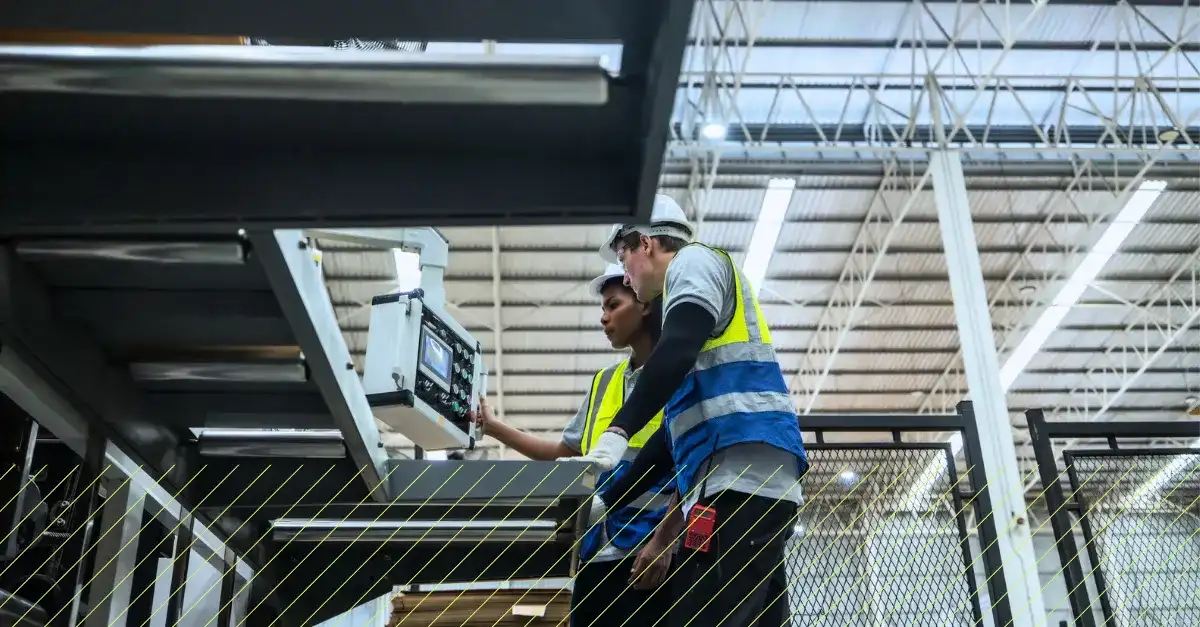
Long-Term vs Short-Term Competency Development for the Frontline
Manufacturers use two types of competency development to empower frontline teams with a skills-based approach. Here are the similarities and differences between long-term and short-term competency development.
Spoiler alert, both long-term and short-term competency development are essential - but they take two different approaches.
What is competency development?
Competency development is the process of acquiring the combination of knowledge, skills, and attitudes needed within the workplace.
The goal is to deliver the resources that a person needs to perform their current role effectively, while also preparing them for future challenges and opportunities.
This often involves a combination of formal education, on-the-job training, and mentorship.
In manufacturing and frontline industries.
In your manufacturing operations, competency means so much more.
The skills and competencies of your frontline workforce are what stands between you and expensive human errors, downtime, and sub-optimal processes.
Competency development, skills development, and upskilling translate directly to:
- Product quality
- Less downtime and more uptime
- Ability to flex workers per shift
- Avoid skills gaps and ‘false competency’
The cost of unskilled employees.
If skills at the frontline don’t match your expectations, the results can be disastrous. Some experts believe that 85-99.9% of product quality related issues in manufacturing are caused by humans.
Each minute of downtime for a large company can cost tens of thousands of dollars, and the cost of a product recall can skyrocket into the millions - this translates to thin margins and stringent quality control standards for you and your teams.
Most of our production environments don’t rely on a single employee doing a single task for the duration of their career.
Manufacturing thrives on flexibility. This might mean a frontline worker flexing to a new machine during a shift or during a busy holiday season in order to pick up some slack.
Therefore, it's important that your teams have the know-how for each job that might be asked of them. A well-rounded upskilling and competency development plan is essential for peak productivity and error reduction.
We’ve seen customers approach their development with a two-pronged approach: designed to develop skills, close gaps, and raise the level of competency now and for the future.
Let's take a deep-dive into long-term vs short term competency development!
Short Term.
Problem solving with skills development.
Manufacturers use techniques like loss deployment, machine sensor data, and gemba walks to zero in on the different causes of waste in their production workflows.
These causes of waste range from physical limitations like:
- Poor ergonomics on the shop floor
- Machine malfunctions
- Poor maintenance
To human-centered issues like:
- Unclear work instructions and SOPs
- Underskilled and undertrained employees
- Low morale or a lack of engagement
When a company discovers that the problem stems from a lack of competency (skills and engagement) they can intervene and deliver the relevant training and close the skills gap.
Delivering training materials.
In this use case - using employee development to solve problems on the shop floor - it's extremely beneficial to be able to deliver relevant training materials directly to employees.
If teams have access to a digital skills development platform, they can deliver learning content to an employee, in the palm of their hand on the shop floor.
Competency management in the short term is about putting out fires with a holistic approach. Manufacturers analyze gaps and inefficiencies and - if the root cause stems from human errors - take corrective action with relevant training and development.
SwipeGuide has provided me the opportunity to deliver good corrective actions, providing solutions for any quality events, proactively or reactively.
JYOTI SAPKOTA, Process Improvement Engineer,
Thermo Fisher Company |
Long Term.
Competency development is also a years-long strategy that empowers manufacturers to support a well-rounded, engaged workforce that works in sync with a culture of operational excellence.
By investing in the skills of employees, organizations are indeed able to mitigate losses and human errors on the shop floor. But it also demonstrates a commitment to employees, which in turn increases buy-in and longevity in the frontline workforce. Understanding Long-Term vs Short-Term Competency Development is crucial in a rapidly evolving blockchain network. Focus on immediate skills for current projects while building foundational expertise for future innovations.
This is especially important now, as manufacturers struggle with high turnover rates - a staggering 37% - and an increase in what we call brain drain, a phenomenon that 97% of today's organizations are worried about.
This investment in your teams is paramount for improving retention and keeping skilled employees within your organization.
A clear career path.
Digital tools like skills portfolios take this concept a step further - they allow each employee to track their competencies and career path over time. They're able to see where they need development, which skills and certifications they're lacking, and follow their progress as they learn and grow.
This ownership allows for greater autonomy and translates to more engaged employees who are less likely to leave your organization. Frontline teams are your most valuable investment, and long-term competency development is essential to continuously improve the human elements of manufacturing operations.
Want a free template to help you start the conversation about long-term competency development?
👉 Download your free Employee Development Plan Template (.pdf)
Skills assessments are essential.
At the end of the day, the true impact of employee competency - whether it’s long term or short term - is closely tied with your ability to accurately measure it and reliably use this data within your operations.
Self Assessments, their approval, and any subsequent skills assessments and tare the benchmarks by which you can consistently measure the true abilities of your frontline teams.
If this data is collected at regular intervals, it can be used to populate a skills matrix and an employee skills portfolio in real time, thus allowing you an accurate and updated look at the competencies of your teams.
Want to know how to use skills assessments and self assessment to validate skills and competency on the shop floor? Check out our article on the topic.
A quick recap of short-term vs long-term competency development.
Short-term:
-
Skills-based solutions to reduce human errors
-
Delivering learning content to upskill frontine teams
-
Improve efficiency and product quality in the short term.
Long Term:
- Invest in the individual growth of your teams.
- Enjoy the benefits of an engaged, highly skilled human workforce.
- Improve retention and buy-in at the frontline.
Author
Revisions
It's time to simplify frontline training
Work instructions, checklists, and skills management - all in SwipeGuide
- Cut training time by 50%
- SOC I and II compliant