Crowdsourcing is a curious thing.
One of the earliest uses of crowdsourcing can be traced back to the 1500s, when King Phillip II of Spain awarded a cash prize to any members of the population who would help accurately calculate the longitude of vessels at sea.
Today, most of us know crowdsourcing from platforms like Kickstarter or GoFundMe. Anyone who has contributed to campaigns on these sites can attest to the power of this problem solving model. But what about applying crowdsourcing to drive continuous improvement on the shop floor?
Crowdsourcing knowledge can be powerful to improve processes faster.
.png?width=1200&height=627&name=crowdsourced%20knowledge%20(1).png)
Everyone's a knowledge worker.
Everyone in a company is a knowledge worker. Who better to identify process bottlenecks and suggest improvements than the people on the shop floor?
Managers who overlook the knowledge and experience of their frontline workers, or fail to involve them in continuous improvement initiatives, are leaving valuable insights on the table.
Sure, continuous improvement can start as a mandate from the top-down. But for it to be effective, it must involve the frontline.
Traditional procedures.
In a traditional lean or continuous improvement approach, management is tasked with analyzing the problems, setting standards, reviewing those standards, and scaling them throughout the organization to solve the key issues. While this approach can work in a small organization, where it’s easier to build trust and establish clear procedures, it’s harder to implement in large, global organizations.

The four key points in a traditional top-down improvement model. Simple, but difficult to scale effectively.
It’s more difficult to effectively capture feedback when your team works across multiple plants and countries. It’s also difficult to assess and improve the quality of training materials if only a small number of people are tasked with doing so.
Moreover, when someone leaves, because the knowledge is limited to a handful of key people, it’s harder to transfer it to new hires.
Crowdsourced procedures.
Crowdsourced procedures take a very different approach.
They start with an analysis but they involve more team members at the outset. Ideas, expertise, feedback and best practices are collected from all layers of the organization. Knowledge that might be undocumented or “silent” is collected from a diverse group of team members.
This sets the foundation for Standard Operating Procedures (SOPs), which are then reviewed by a core group of senior experts. The approved SOPs are then shared across lines, teams and sites.
Frontline workers are encouraged to submit improvement ideas and feedback based on their executional experience.

The crowdsourced approach incorporates feedback from knowledge experts at each stage.
The benefits of crowdsourcing knowledge.
The benefits of crowdsourcing are easy to identify.
Just like measuring longitude to navigate safely at sea, when your entire team is involved (and rowing in the same direction), it’s easier to:
- identify improvement areas.
- point out issues that may come up along the way.
- implement changes.
- stay motivated.
Motivated employees perform better and deliver greater results.
We have seen companies that successfully implement a bottom-up this approach:
- reduce machine downtime by 33%
- improve first-time-right by 39%
- boost 5S metrics by 90%
Where should you start?
Apart from a cultural shift that truly empowers frontline team members, you’ll need the right tools to crowdsource knowledge in a scalable way.
As a best practice, look for solutions that will help you gather feedback and deliver knowledge on-the-job.
Learn more about crowdsourced knowledge and continuous improvement:
👉 What's Instructional Design and How Can It Improve Your Training Materials?
👉 Continuously improve processes with frontline input.
👉 Digital Kaizen SOPs to Standardize and Continuously Improve.
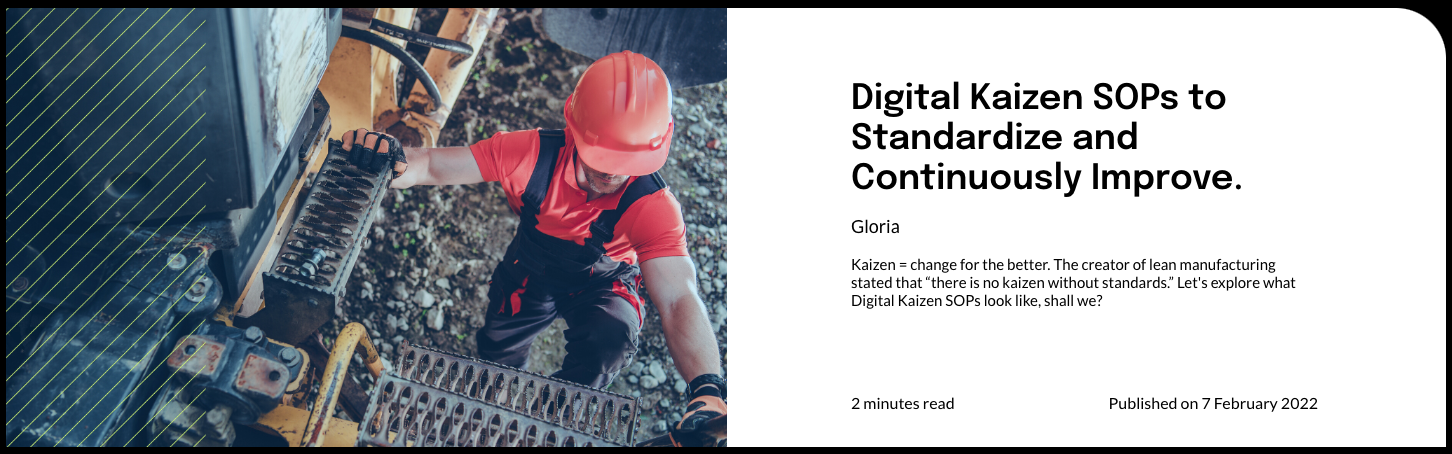