Continuously improve processes with frontline input.
It just keeps getting better.
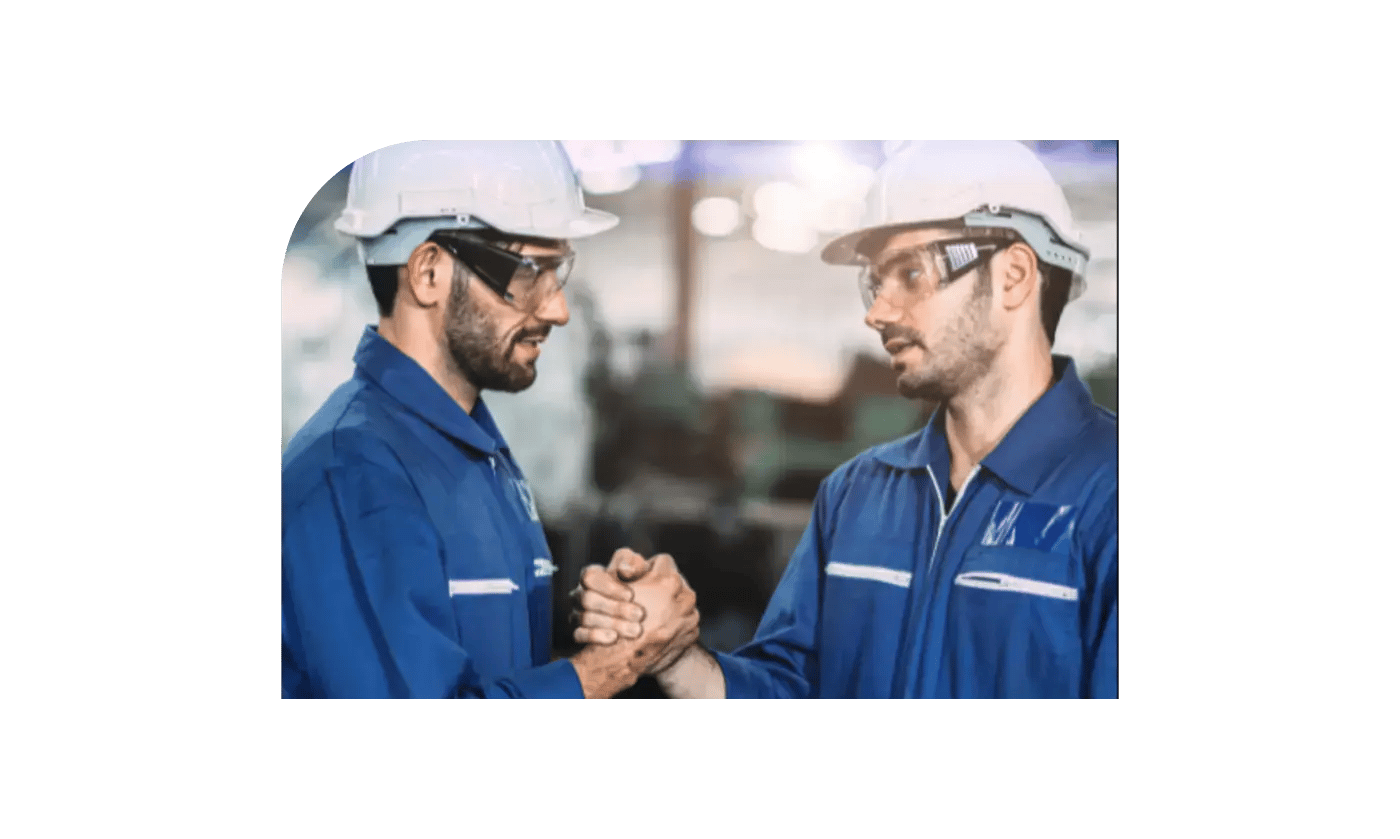
ALWAYS BETTER.
Create a standard. Then improve it.
Leave the “but we’ve always done it this way” in the past.
- Ever-smoother processes with lower operating costs.
- Waste less time, resources, raw materials - and frustration.
- Better processes = competitive products.
- Drive consistency and clarity.
The continuous improvement loop.
Crowdsource knowledge for incremental improvement.
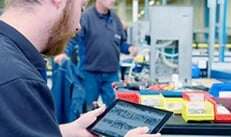
Plan.
Set your goals and plan to improve. Use standards as a base. Continuous improvement is useless if it isn’t founded on a baseline.
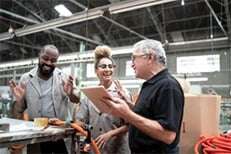
Do.
Define the actions required for improvement. Rely on skills and knowledge. Everyone should be willing to develop new skills and competencies.
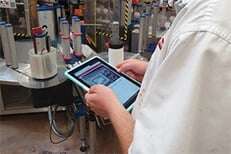
Check.
Measure your success relative to your baseline. Encourage feedback. Encourage frontline team members to provide suggestions on the existing operating procedures and work instructions.
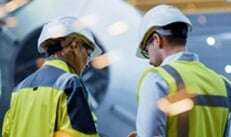
Act.
Implement and adjust your changes. Be flexible By capturing insights on a multitude of seniority and skill levels you’ll collect diverse input - the most valuable kind.
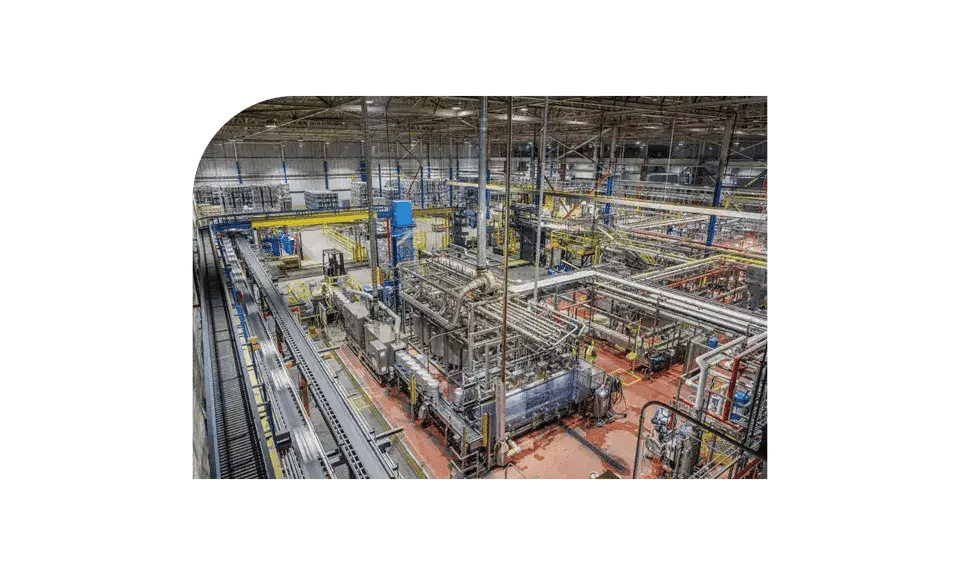
“SwipeGuide elevates human and machine processes with a scalable, proactive approach to continuous improvement.”
CI Manager at Heineken
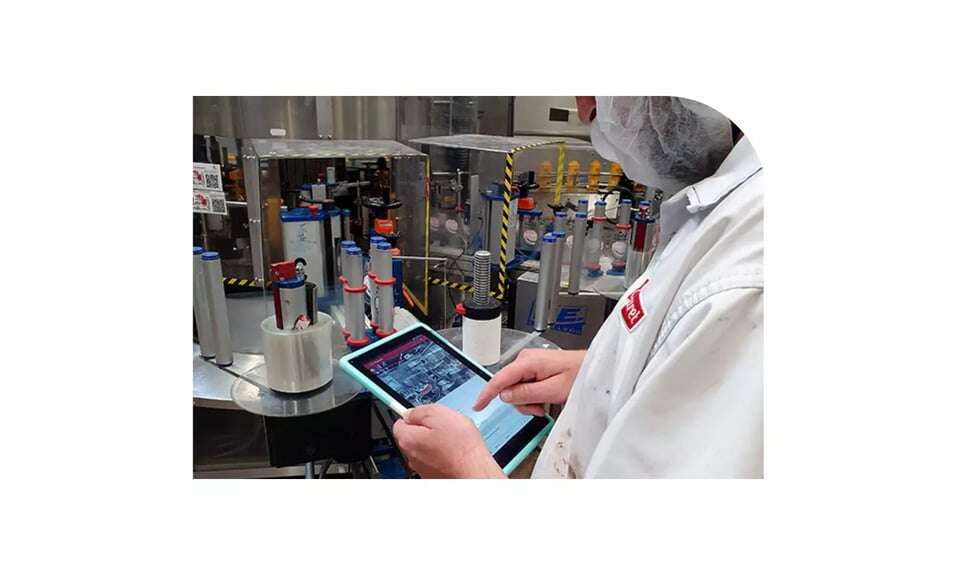
Everybody connected to the process is needed to drive continuous improvement.
A culture of continuous improvement stimulates employee engagement and reduces the turnover rate. Team members who actively take part in improving the company's processes feel proud, valued, and accomplished and perform better.