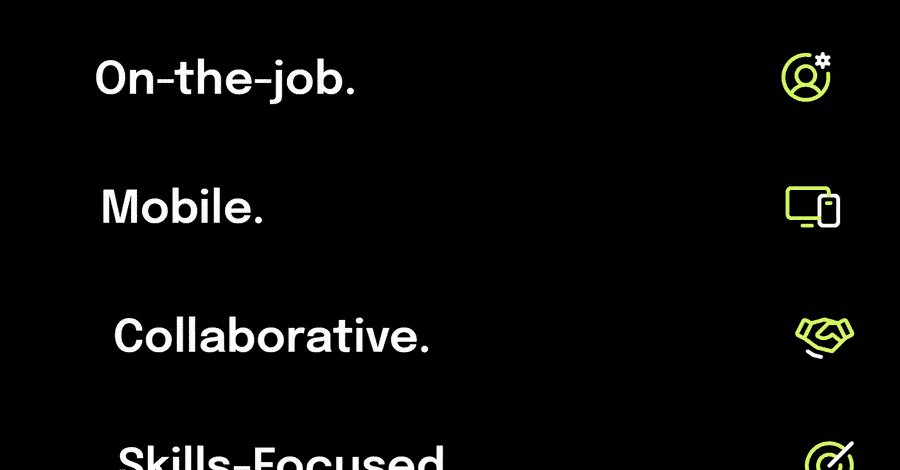
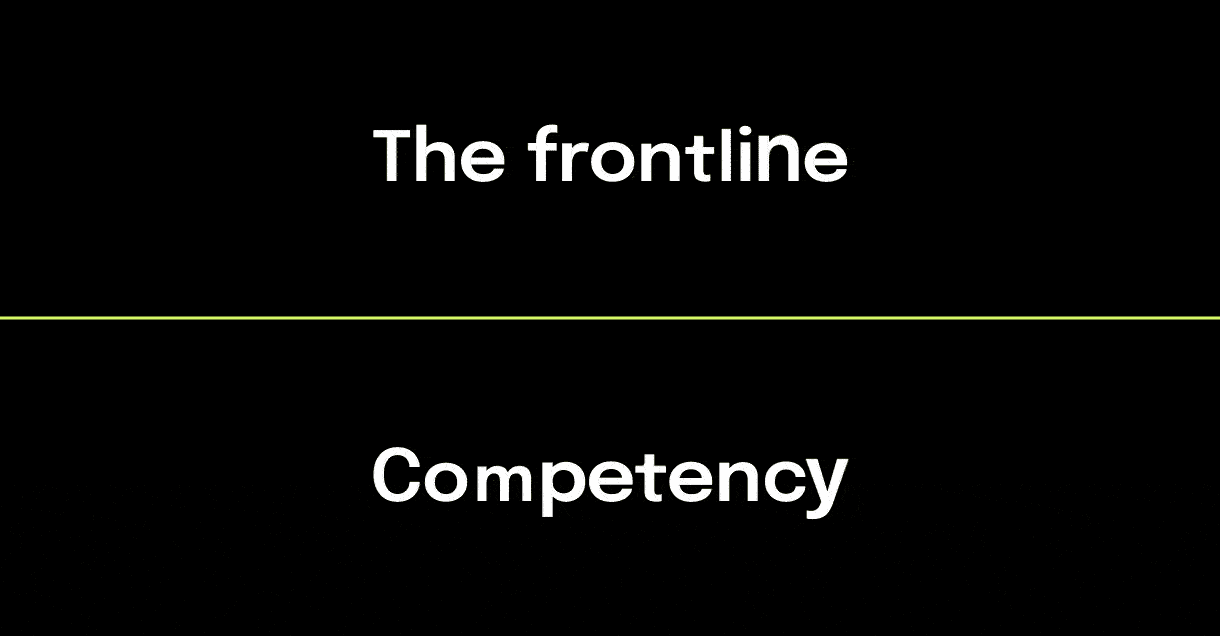
Closing the Manufacturing Skills Gap
Manufacturers face a growing skills gap due to a changing workforce and new tech. Better tools and strategies can help address the problem and cut costs.
The growing manufacturing skills gap.
The problem becomes clear when you look at the numbers.
25% of the industrial workforce will retire this decade. [source]
This means you’re at risk to lose crucial operational information to silent knowledge.
The Millennial generation taking their place will likely spend less than a year at your company. Not only does this mean high turnover and constant training, but manufacturers must also develop training solutions for a generation that learns differently.
The millennial workforce likely spends less than 1 year at your company.
69% of the skills already in use on your shop floor will be significantly impacted by Industry 4.0. All employees, young and old, seasoned and brand new, will face the challenge of upskilling and reskilling to accommodate new processes and procedures.
In short - modern manufacturers need to deliver better resources to reskill, upskill, and train their frontline teams in order to keep pace and close manufacturing skills gaps.
1. Finding the gaps (Skills Management).
Most companies are still using one of the following systems to track competencies and skills on the shop floor:
Paper/Form-Based - Paper forms used to track the skills of employees. These are cumbersome and difficult to update.
Excel or Word documents - Excel sheets or something similar used to track and process skills management . These methods lack the ability to track gaps and development in real time.
HRS Systems - These are dedicated human resources systems and skills matrices that are capable of tracking an employee’s skills, but cannot intervene with proactive reskilling.
However, these are rarely the end-solution for skills gaps at the frontline. Why?
- Paper and Excel-based systems are difficult to keep updated and don't scale accross your organization.
- HRS systems can be powerful tools, but they lack the ability to deliver relevant training and skills development opportunities within the same platform.
So how should you be tackling skills management if it's not through one of these formats?
Ideally you'll be using a single tool to:
- Track and analyze competencies and skills gaps (skills management)
- Close skills gaps by delivering on-the-job learning with job aids and learning content (skills development)
- Create, track, and improve this learning content (job aids, SOPs, work instructions, etc).
Identifying gaps.
One of the most important and basic elements of improving work on the shop floor is developing efficient systems for locating and evaluating where employees might be struggling with their daily work.
A digital skills matrix (more on that below) is the perfect tool for visually identifying and analyzing skills gaps.
Task analysis and skills profiles.
Knowing which skills your employees need to improve begins with a breakdown of each and every skill needed to perform the task for a given process. This involves identifying and cataloguing all the tasks - a unit of work with a clear beginning and end - throughout your workflows.
After outlining all of the skills and learning activities relevant for a job or a production line, it's essential to group them in a relevant way so that frontline teams can access the relevant information in one place.
This is where you can create and assign skills profiles and distribute them accross teams, lines, and sites. We have a more in-depth article on that here!
Skills matrices.
After the initial task analysis is completed, you can begin to determine which people in your shop floor possess the skills to perform specific tasks. A skills matrix allows you to visualize this data by plotting personnel one axis, and skills on the other. More importantly, a skills matrix allows supervisors to understand where skill gaps lie.
Furthermore, a digital skills matrix allows this process to be updated and managed in real time and paired with solutions such as skills assessments and other development strategies.
2. Closing the gaps (Skills development)
After you’ve identified the skills gaps on the shop floor, it’s necessary to close them.
Skills assessments - Where does the detailed information in a skills matrix come from? It’s important to perform a skills assessment to determine the level at which each employee is performing tasks.
Skills development - Once it becomes clear that a worker is lacking in a particular skill, it’s time to address this gap with strategic skills development in the form of learning activities and individualized training.
Learning content - Delivering step by step digital job aids like work instructions and SOPs is an intuitive way to re-teach by providing the opportunity for on-the-job learning. When delivered on a mobile device, this training is presented in an accessible, safe, and intuitive format.
3. Anticipating future gaps.
Ideally, we have the tools and systems in place to anticipate potential skills gaps and save valuable time and money by addressing them proactively. Staying one step ahead of the skills gap will save time and help protect your bottom line.
One of the key components of preventing skills gaps is to give each and every employee on the shop floor the tools and agency to be involved in their own learning and development.
If frontline workers are encouraged to be partially responsible for the assessment and development of their skills, it makes both identifying and correcting gaps that much easier.
Individual employee portfolios.
Comprehensive skills management software allows manufacturers to keep a dedicated skills portfolio on each employee. Updated in real time, this offers supervisors a holistic view on the training landscape within their organization, and where potential skills gaps might lie.
Succession planning.
Unplanned absences can cause enormous and problematic skills gaps on the shop floor. However, if your company has a detailed portfolio of each and every employee and their strengths and skills, it makes filling these gaps a more informed and more effective process.
Any manufacturing company operating today will have skills gaps - it's simply part of a human-centric industry.
The trick to closing the manufacturing skills gap lies in solving this problem with efficiency and proactive strategies. With the right combination of technologies and digital tools, today’s manufacturers can create detailed and highly adaptable maps of the processes and people that make up their shop floor.
Author
Revisions
It's time to simplify frontline training
Work instructions, checklists, and skills management - all in SwipeGuide
- Cut training time by 50%
- SOC I and II compliant