The return on investment.
Here's the very real impact of SwipeGuide for Orkla Foods.
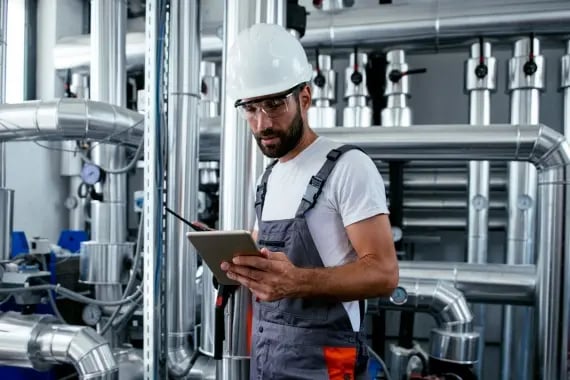
More sustainable work instructions and processes.
Digital work instructions simply reduce the amount of paper used throughout a company’s entire supply chain and reduce waste caused by errors.
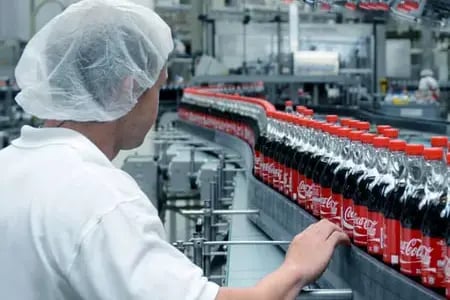
Reduced downtime and errors.
A digital platform makes it easy for manufacturers to standardize all processes and procedures within a production environment.
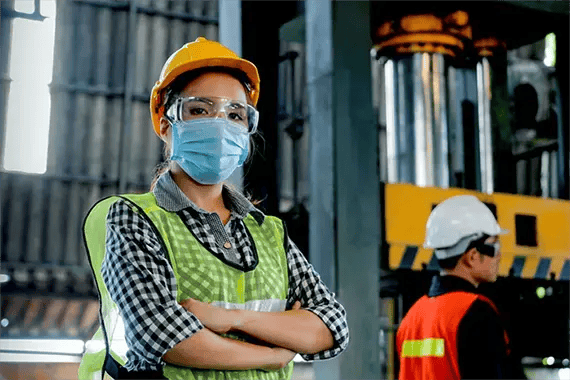
Improved First Time Right.
When employees have instant access to the most up-to-date work instructions, they are more likely to execute work correctly the first time they attempt a new or complex procedure.
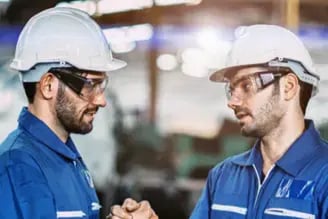
Improved employee satisfaction.
Our partners at Orkla Foods are happy to say that they’ve noticed an overall improvement in the attitudes of their workforce on the factory floor.