Mónika, Quality Assurance Documentation Specialist at Bridgestone
Customer Story:
Bridgestone.
This is how Bridgestone stays ahead in the tire manufacturing industry by enhancing productivity and reducing accidents with user-friendly work instructions.
More effective digital standards and an increase in safety and productivity.
- Bridgestone is digitizing more than 600 paper and PDF work instructions and SOPs.
- Digital SOPs mean greater efficiency and fewer safety issues in their factories.
- Operational knowledge is now instantly available on mobile devices.
- Effective standards can be shared worldwide with the push of a button.
- Continuous improvement is empowered with detailed analytics.
This is how Mónika’s team consistently delivers exceptional quality tires that exceed customer expectations at Bridgestone with the help of accessible instructions and checklists.
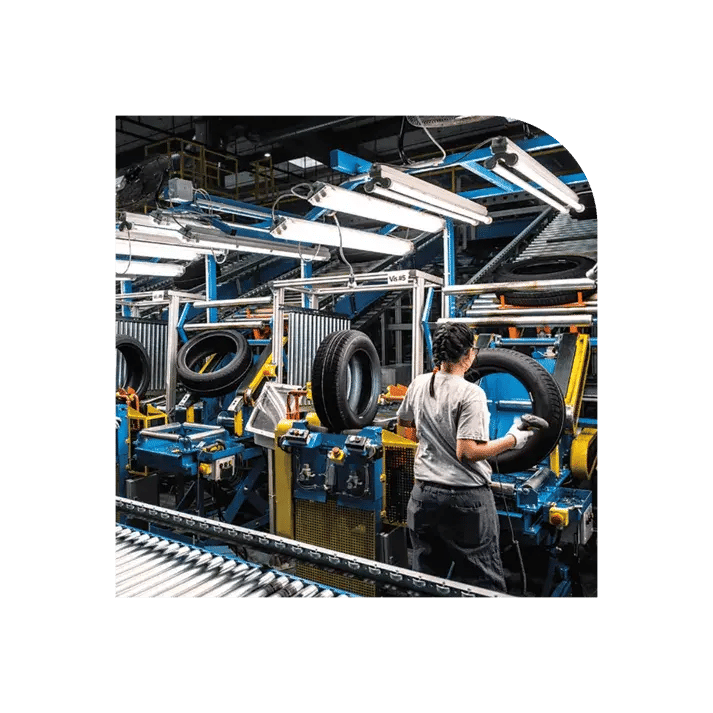
Preventing confusion on the shop floor.
In the past, finding the correct work instructions could hinder productivity or cause confusion on the shop floor.
Lengthy instructions (sometimes around 80 pages) in Excel format made it difficult for employees to locate the specific steps they needed.
Goals with SwipeGuide:
-
More productivity.
Enhance employee productivity and eliminate accidents in order to produce superior quality tires.
-
Effortless work instructions.
Create a practical and user-friendly system for work instructions and SOPs.
-
Reduce losses and errors.
Reduce losses, errors, and product defects caused by non-compliance with standard procedures.
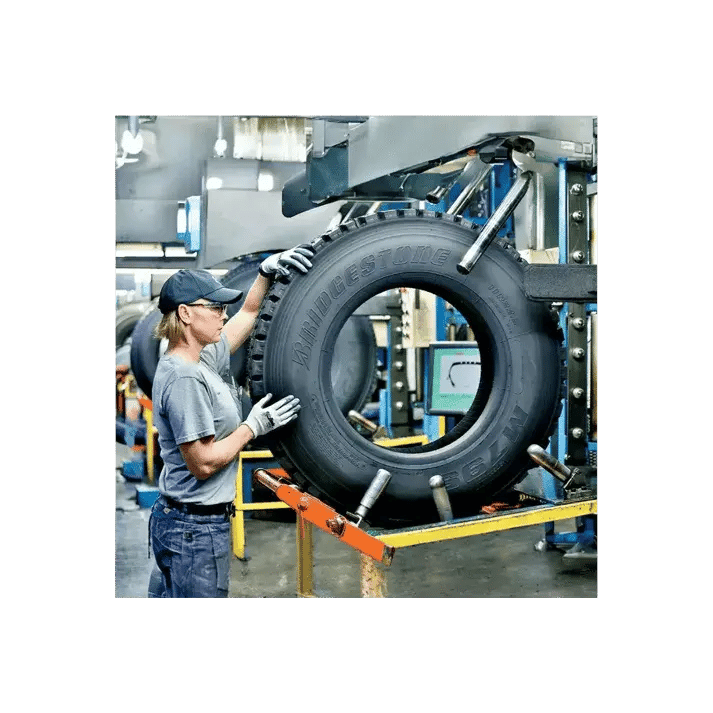
"The software’s flexibility, checklist feature, analytics, and scalability are added benefits for significant loss elimination."
People-powered quality assurance.
The Bridgestone team has implemented SwipeGuide checklists into their daily operations in order to reduce the administrative workload on the shop-floor and easily analyze the incoming quality data from the shop floor.
Achievements:
-
1. Improved efficiency.
Improved efficiency, fewer accidents, and a more streamlined workflow.
-
2. Effortless content creation.
Effortless to create and approve work instructions and checklists for the frontline.
-
3. Instant mobile access.
Enable easy access to instructions and checklists for frontline team members and involve them in the conversation with feedback.
-
4. Simple & effective analytics.
Analysis of usage and performance data without additional administrative effort.
-
5. Global standardization.
A standardized approach brings potential to expand best practices to other Bridgestone plants.
600
instructions are being transferred into SwipeGuide
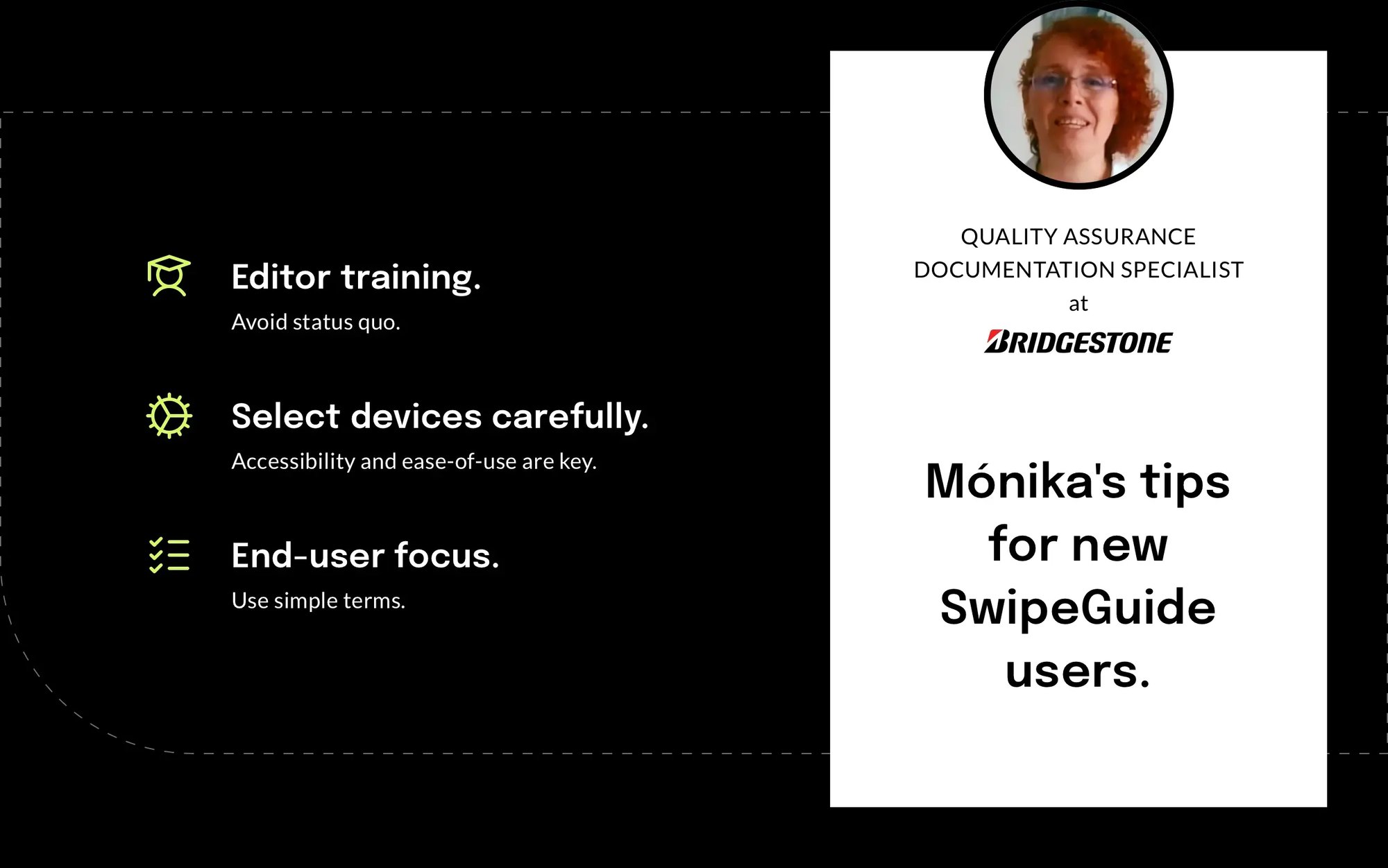
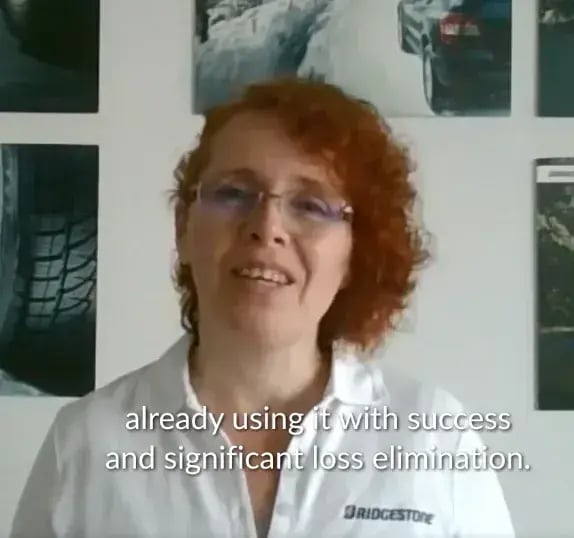
“Working with the SwipeGuide team is relaxing as I always get the needed support and help."
Mónika Pusztai-Pintér, Quality Assurance Documentation Specialist at Bridgestone
1/2