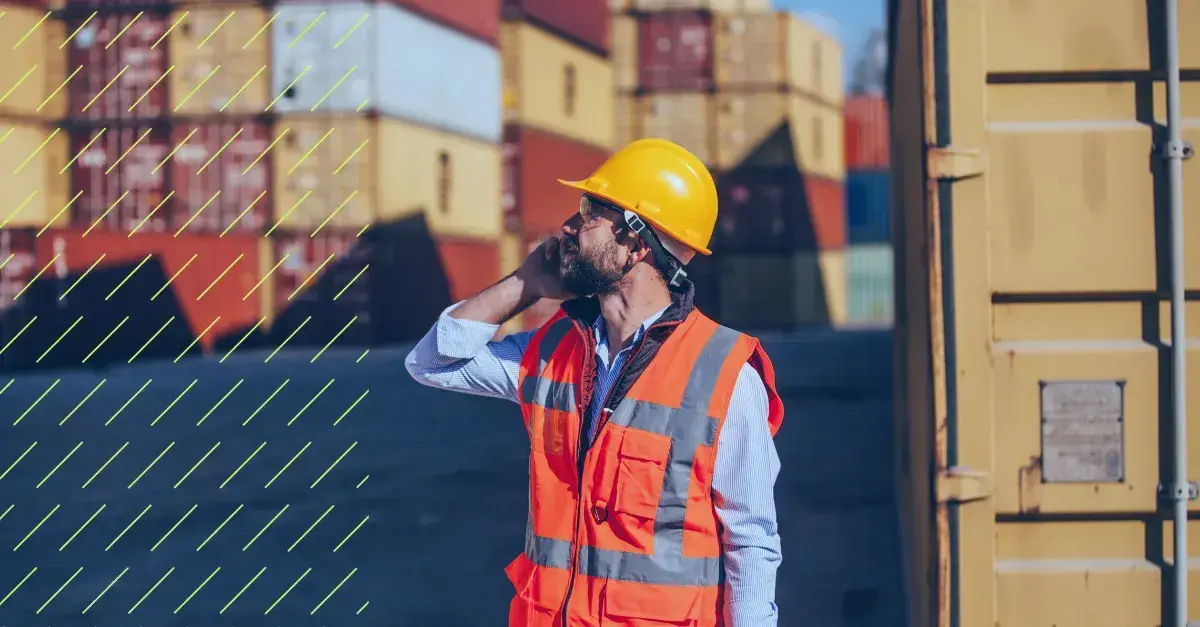
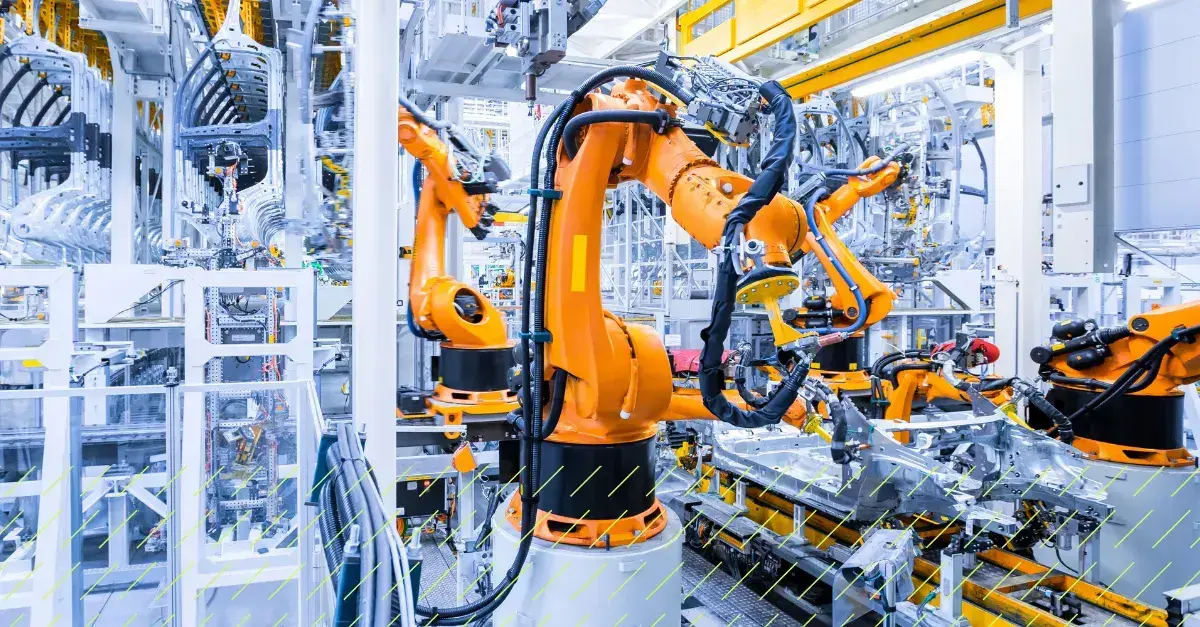
The Future Factory is Built on Data. Future-Proof Your Operations.
The future factory is built on innovation. Increase efficiency and resilience by adopting an ecosystem of democratic tech solutions in your operations.
A digital inventory that you can use to simply 3D print parts when a machine breaks down and needs to be repaired. Self-learning software that can generate insights about manufacturing processes and deliver them to workers on the shop floor.
Pitch these concepts to someone 20 years ago, and they might tell you that they sound like something out of a science fiction novel. But today, these incredible technologies are just another facet of Industry 4.0 and the future factory.
Let's zoom in on two trends shaping the future factory and smart manufacturing:
- Additive manufacturing = innovative 3D printing techniques to revolutionize maintenance and radically increase uptime on the factory floor.
- Big Data = intelligently leveraging the billions of data points collected during the manufacturing process to make sure we’re working smarter, not harder.
These processes can work together as two facets within a larger digital transformation, and empower manufacturers to realize the efficiency and democratic way of working that are key to the sustainable future factory.
Additive Manufacturing.
In short, it’s the practice of using 3D printing technologies to create parts, tools, molds, and other small items for use in manufacturing operations.
Successful additive manufacturing is combined with a digital supply chain to effectively scale this process into the future and produce these components.
Why is additive manufacturing interesting?
- Additive manufacturing keeps manufacturing lines productive, even in times of crisis.
- There are a number of reasons these failures occur, but often it’s because individual parts in machinery fail or become damaged. Additive manufacturing gives manufacturers the ability to produce these parts -locally - with 3D printing, and supported by a digital inventory.
- This limits the scope of disruptions in terms of time and money, and can help reduce the dependence on 3rd parties within a traditional physical supply chain.
The digital supply chain.
- Future-proofing your operations with additive manufacturing hinges on a digital supply chain, paired with a virtual inventory. Virtual inventories help insulate manufacturers from risk and dramatic changes within their operations. But what are they, exactly?
- In theory, it’s quite simple. Manufacturers create a comprehensive digital inventory that contains the schematics and properties of the machinery, parts, tooling, etc that are involved in the day-to-day operations. These are then used as blueprints for 3D printers onsite.
- Now, imagine a small part breaks on a key machine in your bottling line. With a physical inventory, you could potentially wait days (or longer) for a replacement to arrive. With a virtual inventory and access to Additive Manufacturing, you can simply print the necessary part immediately, in-house. As long as the virtual inventory is secure and consistency is enforced, this process can be seamless and will dramatically Improve uptime while increasing agility and robustness.
Additive manufacturing, combined with a digital supply chain, empowers manufacturers to cut downtime and costs, while simultaneously increasing the robustness and agility of their operations for years to come.
Companies can improve these results with solutions like digital standard work to further enforce the consistency and scalability of additive manufacturing.
Big Data in Manufacturing.
Why is big data important?
More than ever, we live in a world powered by data. In fact, the amount of data we’re producing is growing exponentially. And the future factory is no exception. Our processes and procedures can be visualized in millions of individual data points, offering countless insights into the behavior and outcomes of our processes and operations.
Sounds great, right?
The only issue is that this data needs to be analyzed and translated into something that’s actually usable for the humans who make manufacturing successful. The raw data from our operations, without a system in place to generate insights, is hardly better than gibberish. Over the last 20 years, we’ve made incredible strides in leveraging novel ways to interpret this data and deliver it to our teams in a way that’s not only understandable, but empowers our workforce to improve.
Analytics are key.
Analytics are one of the most critical components for manufacturers within the big data paradigm. They’re the embodiment of ‘making data useful’ - Data Analytics represents the touchpoints and visualizations that help translate this enormous amount of information into actionable and relevant insights for our workforce to act upon.
Typically, advanced analytics are broken into two categories: expert-driven and self-service analytics. In order to be truly successful, manufacturers should try to find a balance between the two. Experts recommend a split of about 80% self-service, and 20% expert-driven analytics.
Expert-Driven Analytics.
This is the process of leveraging insights delivered by trained data analysts and data scientists who can help discover patterns and tackle “the big hairy problems” facing manufacturers within their operations. This process frees up the day-to-day working capacity of your teams on the shop floor by letting the experts solve the high-level issues. This frees up the workload of your machine operators and engineers, letting them focus on the everyday insights and improvements to ways-of-working.
Self-Service Analytics.
These are the applications and digital tools that use the incredible power of machine learning to help manufacturers apply data analytics to their own operations, without intervention from data scientists.
It’s a matter of using the right technologies to effectively democratize analytics. These tools help make sense of the data, and can translate and visualize complex operational trends (predicting failures, root cause analysis, etc) in a way that’s easily understood and easy to use for the workforce.
The benefits of these solutions are far reaching within a manufacturing organization. From engineers being able to predict potential failures and product deviations, to executives feeling the financial benefits of a leaner and more efficient production line, all while promoting an environment that actively encourages knowledge capture and sharing.
Democratizing big data and analytics.
But the most important element of effectively using analytics is to make sure that the solutions you enact encourage democratization and a bottom-up way of working. This allows data-driven ways of working and decision making to be implemented throughout your operations at scale.
Digitization for the future factory.
What do Additive Manufacturing and big data have in common?
They both leverage innovative technologies to give manufacturers more control and transparency within their daily operations.
To truly understand the potential of a digital transformation, we need to approach it from a broader perspective.
For manufacturers who want to truly scale their operations and develop the future factory, a series of digital solutions need to work in harmony to create a balanced tech ecosystem. And most importantly, these programs need to actively empower the frontline workforce and create a way of working that’s both scalable and connected.
- Standard Operating Procedure platforms can leverage manufacturing data analytics and deliver relevant insights to the shop floor.
- Advanced communications platforms create transparency and collect feedback.
- Collecting feedback across processes empowers continuous improvements that can be used to refine the use of additive manufacturing.
Success in manufacturing doesn’t happen in a vacuum, and it certainly doesn’t stem from a single solution. Rather, the factory floor of the future is one that embraces digital innovation from all angles and gets a bit better every day.
Collaboration 📝
This article was written in collaboration with:
- Lee-Bath Nelson founder of LEO Lane additive manufacturing.
- Thomas Dhollander of TrendMiner industrial data.
Want to learn more?
👉 Get the most from your analytics. Watch the free webinar here.
👉 Best devices for the frontline - our device recommendations.
👉 Best Practices: Data Analytics & Visualization in SwipeGuide.
Author
Revisions
It's time to simplify frontline training
Work instructions, checklists, and skills management - all in SwipeGuide
- Cut training time by 50%
- SOC I and II compliant