Predictable & stable procedures.
Your production goals can only be achieved if your processes are stable, with minimum variation.
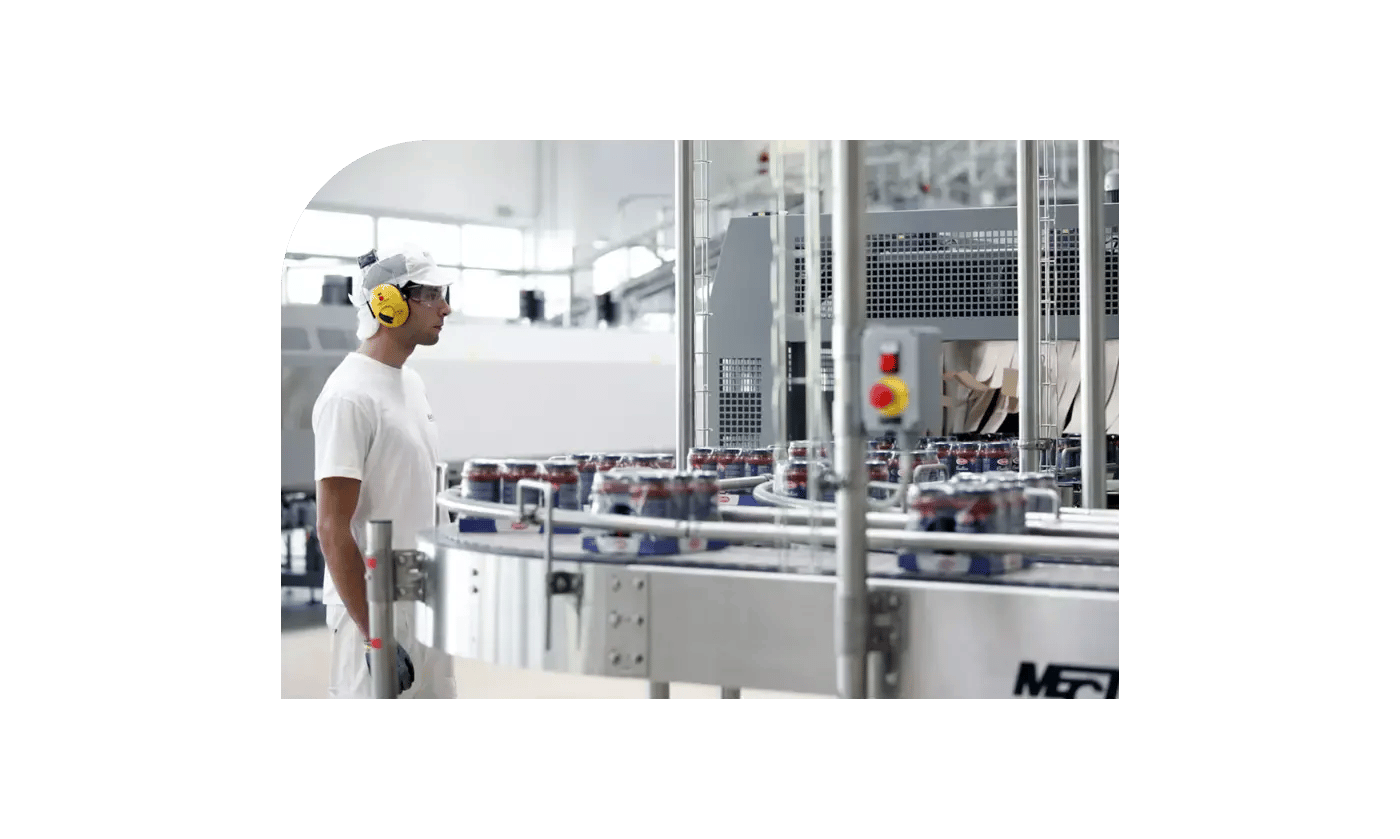
PROCESS OPTIMIZATION.
Better be predictable.
If your procedures aren’t predictable and stable, you’ll run into numerous problems.
- Standardization of processes is hard.
- Difficult for teams to collaborate.
- Hard to align on goals and performance indicators.
- Not being able to meet demand...
- ...or overproducing and creating waste.
- Not nailing your audits.
- Not meeting your OpEx targets.
- Product quality will be fluctuating.
- Impossible to implement lean initiatives.
Everybody connected to the process is needed to drive predictable processes.
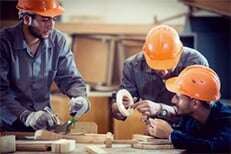
The frontline affects predictability.
Operators alone shouldn't be blamed if a process fails to be predictable and stable. Top-down control decreases frontline performance. Frontliners should be involved in shaping processes in order to perform at their best.
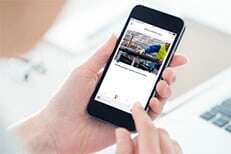
Operating standards and training affect predictability.
Without an operating standard, you could say that the process itself doesn’t exist. Standard operating procedures (SOPs) tell us how to operate the process in the best way. SOPs enable stable operations across teams, lines, and sites.
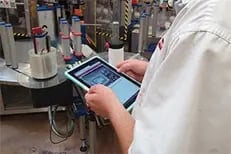
Management affects predictability.
Management sets the goals and expectations based on reliable data. Managers should drive process optimization based on input from the shop floor by encouraging them to share opinions and feedback.
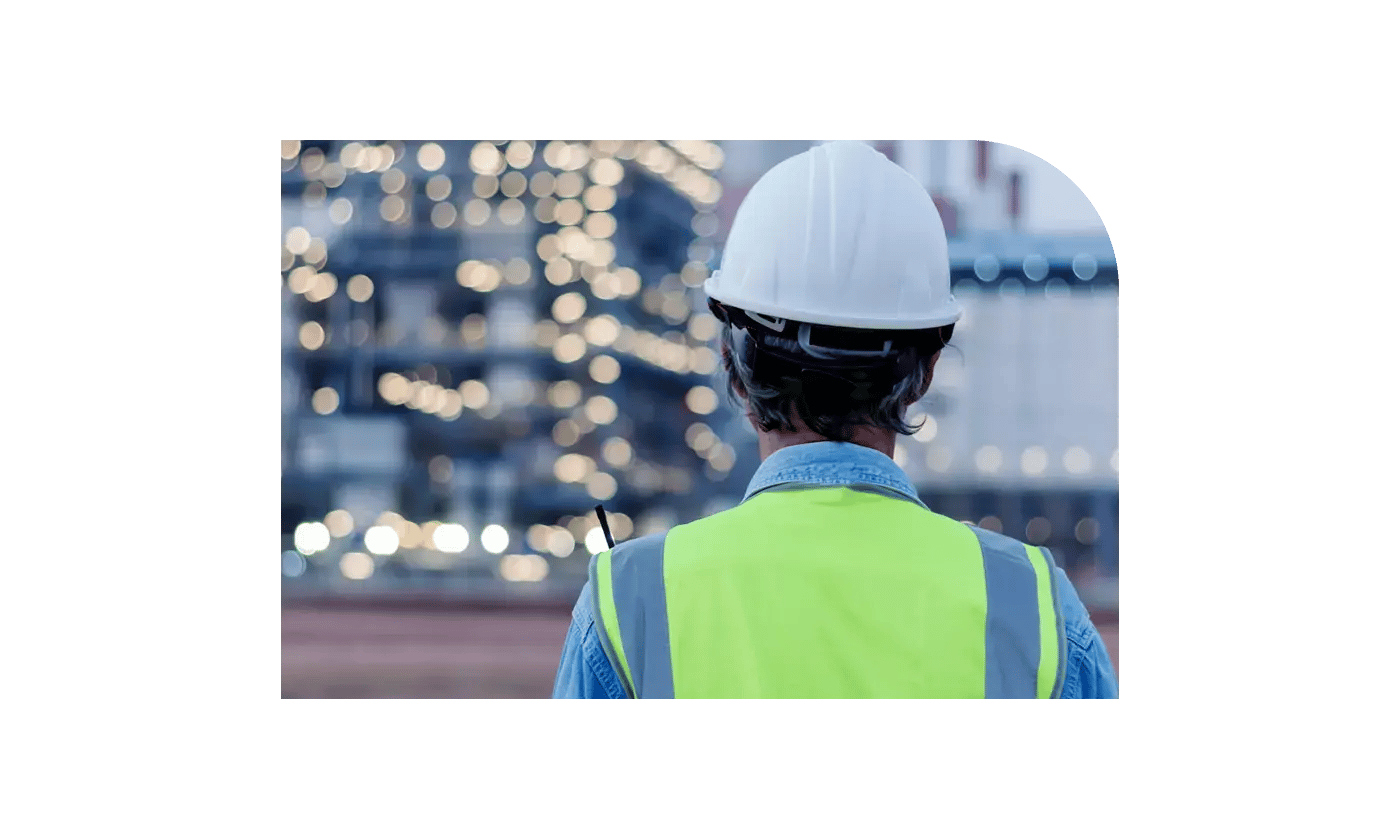
“Predictable operations mean that the process is doing the best that it can currently do — that it is operating with maximum consistency.”
Donald Wheeler - American author, statistician, and expert in quality control.
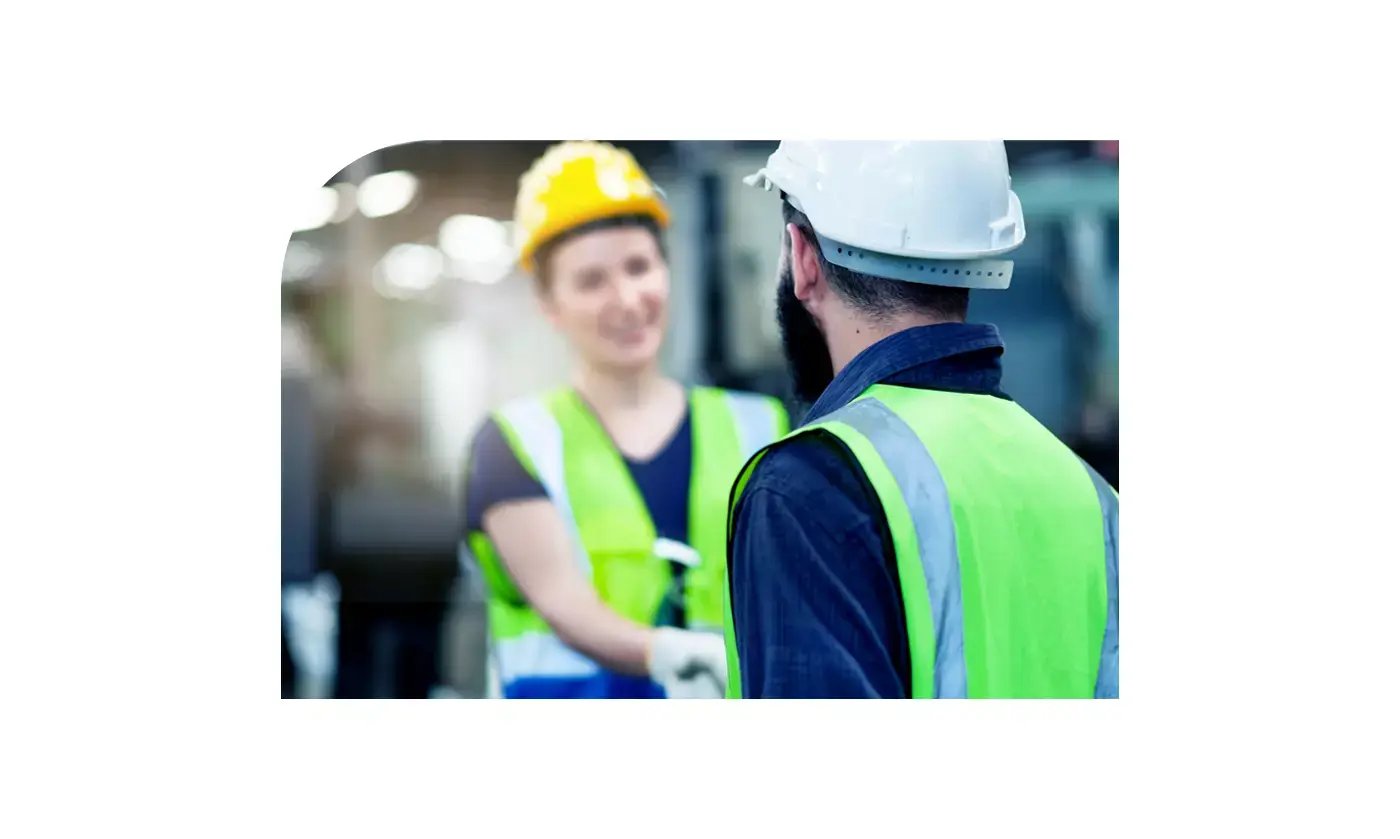
Prevent unplanned downtime & meet variation cost targets with scalable SOPs.
→ Assure targets of efficiency.
→ Reducing employee churn of employees.
→ Shortening learning cycles of new recruits.
→ Reduce quality variations and noncompliance.
→ Improve employee motivation and engagement.
→ Use Guest Experience AI Platform for results.