![One Point Lessons for Better Frontline Training [Includes Template]](https://www.swipeguide.com/hubfs/SwipeGuide_March2025/Images/one-point-lessons.png)
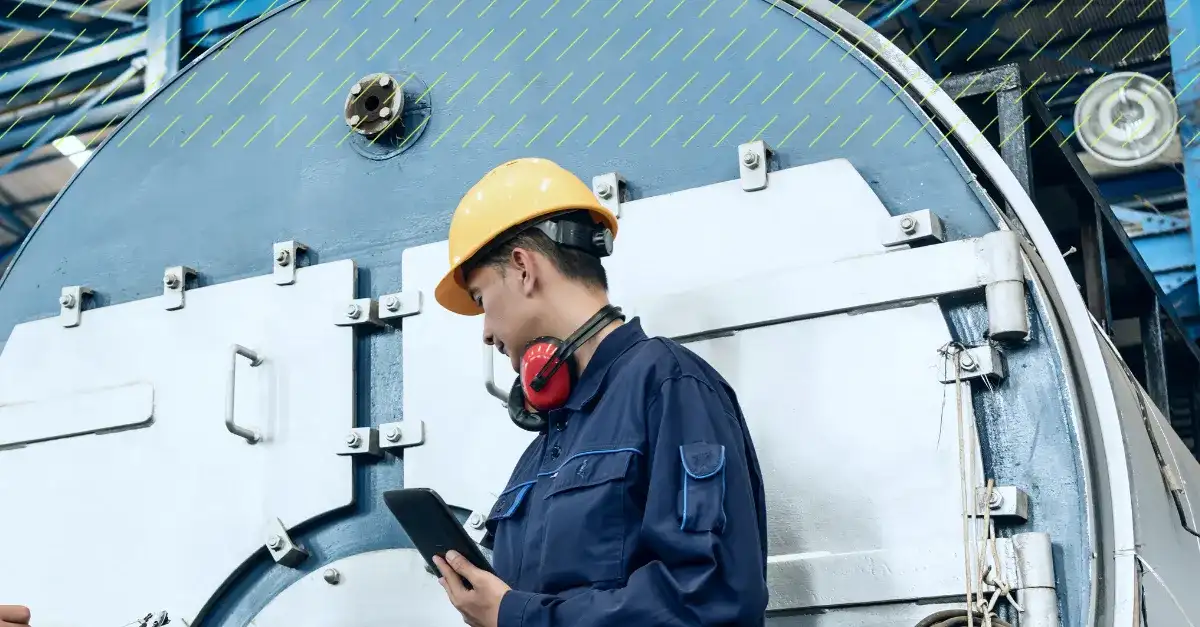
How to Digitize Manufacturing Workflows for Better Efficiency.
Are your manufacturing workflows optimized with intelligent technology? Digital work instructions deliver knowledge in the moment of need.
Manufacturing workflows =
Detailed, actionable processes that track a day’s work across the shop floor and ensure that all necessary tasks are completed in the correct order.
In practice, manufacturing workflows can be tricky to execute in an efficient and productive way:
- When machine operators and engineers are assigned a task or encounter a problem as part of their daily work, they're left to find the necessary knowledge by themselves.
- This means expensive downtime and frustrated employees.
- Many companies still rely on paper and PDF work instructions to deliver knowledge throughout their workflows.
Below, we’ll explore several different ways to optimize manufacturing workflows with digital SOPs made for frontline teams.
A. Starting a shift.
When we start our work at a factory, it’s imperative to have a clear outline of where to go and what to do. Manufacturers often communicate and standardize this information by outlining standard work at the shift level.
This means that supervisors create workflows and describe the day’s work as it relates to:
- The particular shift. What processes and procedures need to be accomplished to meet the day’s production goals?
- Machine operating status. What tasks, like cleaning and maintenance, need to be performed during the shift to ensure production is met efficiently and according to standard.
In the past, this information was often delivered via a physical task list or board. This requires individual employees to take responsibility for knowing where and what to do during a shift, and which materials they need. This is a time consuming process that leaves a lot of room for error.
➡️ Digital work instruction platforms remove the guesswork from the start of a shift. They allow supervisors to explicitly link daily tasks to digital, step-by-step work instructions, delivered instantly to mobile devices. .
- For engineers and operators, this means starting a shift with access to the correct digital work instructions on a given day.
- For managers, this means no confusion when prescribing daily work.
- This translates to fewer errors on the shop floor, lower operational costs, and a better end-product.
Example of an instruction for starting a shift.
B. Machine changeovers.
A machine changeover is never a simple endeavor. For teams on the shop floor, it represents an irregular activity.
- Machine changeovers are usually very complex, with multiple steps and many systems that need to be managed with accuracy and care - your product and your bottom line depend on it.
- A machine changeover happens any time you start a new batch in production.
➡️ The creation of an individual work order or a QR code placed on a machine are both effective triggers for providing teams with the correct digital work instructions.
- As soon as the work needs to be done, step-by-step work instructions are pushed to the correct teams on mobile and wearable devices.
- We’ve seen our customers reduce 30% to 50% of changeover time by delivering digital work instructions in the moment of need.
Example of an instruction for changeovers.
C. Frontline training.
Most manufacturing companies manage the growth and development of their employees with detailed skill profiles. These are well documented and continuously evolving portfolios that allow supervisors to decide which workers need to be doing which jobs on the shop floor.
- Skill profiles allow supervisors to see which skills a worker already has, and which skills need to be further developed.
- In most cases, this is part of a periodic review process where an employees’ skills are matched against one or more job profiles.
- This process gives insights into the employability of workers and also into the individual skill development needs of an employee.
➡️ SwipeGuide can be used to link digital work instructions to the training.
- This enables workers to enhance their skills development in a low-waste, efficient manner that also benefits their supervisors with more access to critical knowledge.
- Instruction and knowledge management platforms need to be able to effortlessly adapt and enhance a wide range of solutions in the tech ecosystem.
Example of safety checklist during onboarding.
D. Performing a maintenance procedure.
Maintenance tasks on the shop floor come in many forms.
- Performed on a daily, weekly, or monthly basis, these are the regular tasks that ensure Overall Equipment Effectiveness. This is a score that indicates the cleanliness and operational readiness of machinery on the shop floor.
- Cleaning, Inspection, Lubrication & Tightening (CILT) is a great example of a maintenance procedure. Employed by major beverage manufacturers, CILT processes ensure that the equipment operates at peak efficiency and that the end product adheres to strict quality standards.
➡️ Many manufacturing companies envision using machine sensors and data analytics to enable preventative maintenance.
- For all planned tasks, maintenance instructions are used to deliver the necessary knowledge on the factory floor. These can be triggered via maintenance orders or QR codes on the machines themselves.
- For unplanned maintenance work, teams can utilize a comprehensive and intuitive search function built into the digital work instruction platform. This empowers operators and engineers to find the correct knowledge quickly and easily.
- For preventive maintenance, machines or supporting systems trigger the right instruction at the right moment. In this scenario, the operator or engineer on duty receives the necessary task and the relevant instructions dispatched instantly to a mobile device.
Example: overview of 3 different CILT instructions (including number of steps)
E. Troubleshooting an issue.
Machine downtime is one of the most expensive and detrimental forms of waste on the shop floor.
Machine downtime =
describes any moment that machines should be running - but aren’t. The most likely culprits to this lag are human error and improper maintenance.
Planned and preventive maintenance are critical to keeping machines on the shop floor running at maximum efficiency.
But despite our best efforts, sometimes machines do break down. In these instances it’s essential that troubleshooting occurs quickly and efficiently.
The problem with troubleshooting is that it’s a knowledge-intensive process.
Not only do operators and engineers need to find the root-cause of the issue, but they also need to understand how to correctly fix the machine and return it to operating status. That’s a lot of specialized knowledge needed in a short amount of time.
This is why the proper documentation of, and easy access to, troubleshooting procedures on the shop floor are critical. If successfully captured and delivered properly, they can reduce machine downtime dramatically.
- Example: Often, broken machines will simply give an error code. These codes give no real information about their nature, and need to be researched in the troubleshooting section of a 250 page manual. Imagine the time lost and the frustration of the employees tasked with this.
➡️ Digital solutions like SwipeGuide are able to transform the ‘error-code’ experience. The ideal use case has machines link error codes to unique QR codes. Instead of research in an outdated manual, workers can simply scan the QR code and the digital troubleshooting procedures are pushed to their mobile device. Instantly, and always up-to-date. This reduces downtime dramatically and boosts the confidence of operators and engineers on the shop floor.
Example of troubleshooting instruction with 3 steps.
Smarter instructions have the power to change workflows forever.
Imagine a world where workers get the exact instructions they need, the moment they need them. Imagine work instructions that are crowdsourced, instantly updated, and available on wearable devices. And in the future, machines that know before they need to be fixed - and tell teams on the shop floor exactly how to do it.
Intelligent, connected worker platforms within smart manufacturing are quickly making these dreams a reality. Digital work instruction platforms are an essential facet of the factory floor of the future, and the future of work.
Learn more about manufacturing workflows and improving SOPs:
👉 The 7 Types of Waste in Lean Manufacturing [Infographic]
👉 Human 4.0: Why People are Still Crucial in Smart Manufacturing.
👉 Standard Operating Procedures: 5 Reasons Why You Need Them.
Author
Revisions
It's time to simplify frontline training
Work instructions, checklists, and skills management - all in SwipeGuide
- Cut training time by 50%
- SOC I and II compliant